Dynamic Temperature Control
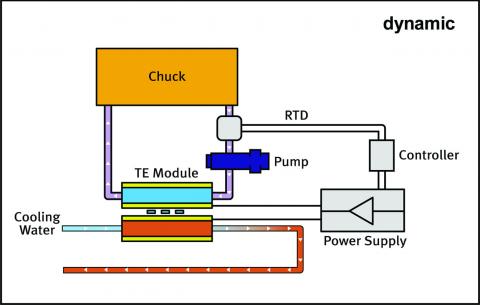
Dynamic Temperature Control is accomplished by sensing the temperature of the process fluid returned from the process chamber (wafer chuck) and varying the temperature of the process fluid supplied to the chamber to compensate for changing process conditions, in real-time.
This will result in through-the-lot uniformity and chamber-to-chamber wafer processing uniformity.
- temperature control at the point-of-use rapid ramp rates equal greater chamber productivity
- compressor-free POU system consumes ~50% less power
- entire system has one (1) moving part for higher reliability
- use of perfluorinated fluids requires no filtration or highly specialized components
- zero footprint with sub-floor mount
- modular system design results in simplified troubleshooting and fast MTTR
Static Heating & Cooling Units
Static Heating & Cooling Units maintain the temperature set-point in a very large reservoir by cycling heaters and cooling control valves on & off, thus consuming about 50% more power than the LAUDA-Noah POU System. The fluid is pumped to the chamber from the static unit's remote location, typically in the sub-fab or 2nd level below the chamber. This distance can be as much as 50-75 feet away from the surface of the wafer. This results in large ambient losses that will vary from chamber-to-chamber, depending on the length of the process fluid hose, the type of hose used, routing of the hose from the sub-fab to the chamber and ambient conditions.
When static units are employed, the wafer chuck will eventually reach a new equilibrium temperature since the static unit is not designed to compensate for changing process conditions.
Dynamic Temperature Control results in process improvement for our customers
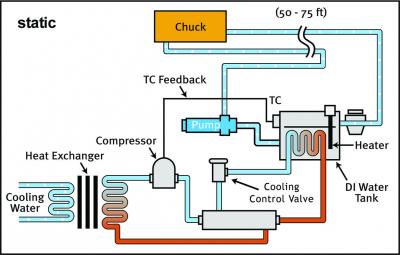
The example below illustrates several key benefits of Dynamic Temperature Control. The charts immediately below illustrate the functionality of a LAUDA-Noah POU system vs. a static heating/cooling system:
- large footprint consumes valuable fab tool space
- large reservoir & long process fluid hose length requires ~6X more fluid than a LAUDA-Noah POU system
- static heating/cooling units typically in remote locations increase cost & decrease efficiency
- compressors and large pumps require frequent maintenance & consume 50% more power than LAUDA-Noah POU systems
The data shown below is from an Asia Pacific wafer foundry. The 300mm chamber temperature profile comparison illustrates the performance of LAUDA-Noah's Dynamic POU system vs. a static unit on a high aspect ratio Etch process. Perhaps the most compelling aspects of this data set are the temperature uniformity and rapid response times accomplished under very high RF power conditions. (~3.8kW) Note the wafer-to-wafer repeatability and constant baseline temperature performance when using the LAUDA-Noah POU system.
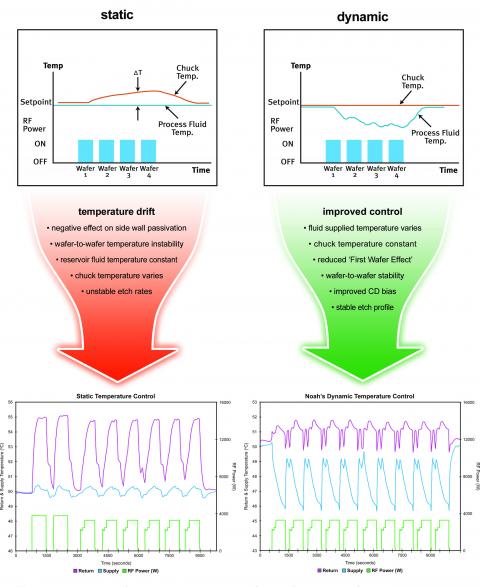
Dynamic vs Static Temperature Control