Not Just Another Chiller
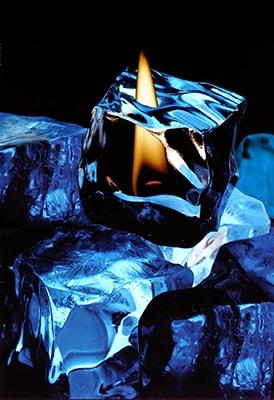
The LAUDA-Noah thermoelectric POU System is "Not Just Another Chiller." The information that follows is the result of many joint efforts on behalf LAUDA-Noah and its Plasma Etch & Semiconductor customers who share common goals: improve temperature uniformity at the wafer, reduce the temperature component of first wafer effect, and reduce overall "chiller" cost of ownership.
Below are five (5) considerations when selecting a Thermoelectric Temperature Control System:
1. All Thermoelectric (TE) chillers NOT alike
Confirmed; TEs' represent only one part of a chiller's design. The switching & control methods used by a chiller will impact the TEs' reliability. The TEs' can switch directly from heating to cooling, or visa-versa. They can switch on & off while in the heating or cooling mode and can increase or decrease the amount of heating or cooling without switching whatsoever.
2. TE chiller close to chamber does NOT equate to dynamic control
The reality is that true Dynamic Temperature Control can only be achieved when all five (5) of the following system design and installation requirements are met:
- fluid set-point temperature is controlled at the return loop
- very small fluid reservoir and process fluid-loop volume (< 1 US GA.)
- heating / cooling elements with rapid ramp rates
- short hose lengths from the POU module to the chamber
- maximized process fluid flow rate
(Therefore, installing a static unit next to chamber will not enable it to provide dynamic temperature control)
3. TCU's do NOT require cooling capacity equal to the process' RF power
Our experience shows that RF power coupling efficiencies for optimally designed chambers are approximately 40 - 45% of the lower RF power and only 5 - 15% of the upper RF power.
All static TCUs require excess cooling & heating capacities due to their very large process fluid reservoirs. The process fuid reservoir on LAUDA-Noah's dynamic temperature control system is less than 1 gallon. We require much less cooling/heating capacity for the same application as a static TCU because of our small reservoir volume.
4. Changing TCU's does NOT force process recipe revisions
LAUDA-Noah will, for a customer's retrofit evaluation, monitor and adjust its fluid temperature control profiles to match an existing TCUs' in order to guarantee a smooth process integration via DAQ.
The LAUDA-Noah POU system's dynamic temperature control design and software gives it exceptional flexibility for process-matching, independent heating/cooling, PID control parameters, independent heat/cool spread and cross-over control values.
5. All wafer process tools do NOT accurately display the temperature of their chambers
More than 10,000 POU installations have proven that temperature monitoring differs according to tool/chamber type, and:
- TC / RTD positions relative to the wafer vary
-
Tool & TCU software calibration procedures vary
- external test equipment not used regularly for verifying
- inline fluid sensor (high RF power) readings displayed
- TCU reports its reservoir temperature on the tool
- calibration and software offset procedures vary per customer/fab